两化融合暨智能制造应用总体现状
双星是一个具有97年历史的老国有橡胶企业。青岛双星是山东省轮胎行业目前唯一一家国有上市公司。2014年,双星开启了“二次创业、创双星世界名牌”新征程,确定了“第一、开放、创新”的发展理念,正在形成集轮胎、智能装备、智能物流(机器人、冷链物流等)、废旧橡胶绿色生态循环利用等产业于一体的国际化企业集团。
公司高度重视企业信息化建设,把信息化建设、两化融合上升到企业发展战略和增强企业核心竞争力的高度来认识,坚持管理创新、技术创新与信息化相辅相成、相互促进,积极推进信息化建设工作,使信息化项目建设切入企业生产经营的核心管理,促进信息资源的深度开发和信息系统建设,加快两化深度融合,提高信息化的质量和水平。
近年来,双星集团全体干部员工认真落实青岛市委市政府环保搬迁、腾笼换鸟、凤凰涅槃的战略部署,借互联网+、中国制造2025、国企改革等契机,变“新常态”为“新抢态”,加速新旧动能转换,主动淘汰了60%以上的落后产能和产品,抢先从“汗水型”走向“智慧型”。率先在行业内推行需求细分化、组织平台化、内部市场化的“三化管理模式”,率先建立了全球轮胎行业第一个全流程“智能制造”智能化工厂,率先创立了开放的“智能服务”和“智能制造”生态系统。
因为创新和智慧转型,2016年以来双星被国家工信部评为全国“工业品牌培育示范”、“技术创新示范”、“质量标杆”、“绿色轮胎智能制造试点示范企业”、“服务型制造示范项目”,不仅是五年来中国所有企业中唯一一家全部获得五项国家级殊荣的企业,也是唯一一个从品牌、技术、质量、制造、服务全产业链试点示范的企业,并被称为“中国轮胎智能制造的引领者”。
图1 双星率先建立了全球第一个全流程“工业4.0”轮胎智能化工厂全貌图
自2014年以来,双星开启二次创业新征程,确立“创双星世界名牌”发展目标和“第一、开放、创新”的发展理念,公司高度重视企业信息化建设,把信息化建设、两化融合上升到企业发展战略和增强企业核心竞争力的高度来认识,坚持管理创新、技术创新与信息化相辅相成、相互促进,积极推进信息化建设工作,使信息化项目建设切入企业生产经营的核心管理,促进信息资源的深度开发和信息系统建设,加快两化深度融合,提高信息化的质量和水平。
为适应公司发展方向从“轮胎密集型产业”向“向绿色轮胎智能化生产”的转型,双星以用户为中心,搭建各种信息平台,告别了应用系统“信息孤岛”时代,为双星信息化事业的发展铺平了道路。双星为“两化”融合贯标企业,并通过工信部第二批绿色制造示范评审,成为绿色工厂示范。同时,双星不断加快创造新动能,推动互联网、大数据、人工智能与轮胎产业的深度融合,促进轮胎产业智能制造踏上新台阶。
积极响应中央供给侧结构性改革号召,坚持推行“以智能化实现模式极简,以智能化实现产品极致,以智能化实现与用户距离极短”的战略方针,整合全球顶尖的“工业4.0”专家和伙伴资源,集成全球最先进的信息通讯技术、数字控制技术和智能装备技术,建立了全球轮胎行业第一个全流程“工业4.0”智能化工厂,搭建了一套由用户(订单)指挥、数据驱动、软件运行的智能生态系统。
图2 双星“工业4.0”轮胎智能化工厂生产线
2016年6月,双星全球轮胎行业第一个商用车胎全流程“工业4.0”智能化工厂全线投产,工厂中的设备包括11种智能机器人80%是双星自主研发和生产的,将人工效率提高了3倍,产品不良率降低了80%以上。
2017年7月,双星全球领先的轿车胎全流程“工业4.0”智能化工厂全线投产。至此,双星成为全球轮胎行业唯一一家同时拥有卡客车胎和轿车胎全流程“工业4.0”智能化工厂的企业。
双星的全流程“工业4.0”智能化工厂中采用了双星独创的MEP智能信息匹配系统,实现物、人、设备、位置的信息智能匹配,解决了全球以液体或粉体为原料的制造企业无法全流程实现智能制造的难题;工厂采用的APS智能排产系统,被德国西门子公司专家称为“全球第二家将APS应用到实际生产中的轮胎企业,走在了世界前列,引领了世界轮胎智能制造的方向”。
项目详细情况介绍
1、项目背景
作为传统的劳动密集型、资金密集型、资源密集型、封闭化和同质化严重的行业,轮胎行业面对智能化、信息化的产业浪潮,正加速淘汰落后产能,向绿色轮胎智能化生产转型。新形势下,轮胎行业到了必须转型升级的时期。
双星集团近年来坚决贯彻中央及省委省政府关于淘汰轮胎落后产能和青岛市委市政府关于环保搬迁、凤凰涅槃的战略部署,认真落实“三严三实”,加速升级搬迁和互联网转型,顶住巨大压力,聚焦在5个字上下功夫:转、调、去、创、建。在行业生死存亡的转折期,不仅较好地解决了转型升级中遇到的难题(观念/订单/资金/技术/产能),做到了搬迁不欠产,而且成为行业中为数不多的销量和效益持续双增长的企业。
近年来,双星颠覆原有的运营模式,由“以产能为中心”调整为“以订单为中心”,使企业真正将发展重心放在满足用户需求、创造有效供给上。此外,为加快推进“智能转型”,双星集成全球最先进的信息通讯技术、数字控制技术和智能装备技术,搭建了全球轮胎行业第一个全流程“工业4.0”智能化“绿色工厂”,融“产品定制化、企业互联化、制造智能化”于一体,搭建一个由用户(订单)指挥、数据驱动、软件运行的智能生态系统。
2、项目实施与应用情况详细介绍
双星正在全速推进“三化两圈”战略,“三化管理模式”是需求细分化、组织平台化、内部市场化,是两圈的基础和保障;“智能服务”(即,远程运维服务)是以工业4.0思维通过智能服务思维建立开放的汽车后市场生态圈;“智能制造”(即,全流程智能制造)是通过双星轮胎建立轮胎及轮胎智能制造装备、方案和标准的制造生态圈。两圈融合形成物联网生态圈战略,推动互联网、大数据、人工智能与轮胎产业的深度融合,促进轮胎产业智能制造踏上新台阶。
1)产品的大规模个性化定制
以“开发用户资源而不仅是开发产品”作为产品开发理念,双星在吸收国际原材料供应商及客/用户参与设计,整合利用国内外技术资源的同时,大胆创新,颠覆行业一产品一模具一施工的传统设计,在行业内首创产品的模块化设计技术,用户通过双星的“创客网”、“星猴网”(图2)等交互平台参与交互、设计,进行个性化定制。“星猴快修”第一时间对用户个性定制的产品进行上门服务,并对轮胎的使用情况随时跟踪,适时保养,为用户提供全生命周期的智能服务。
图3 创客网及星猴网
2)建设轮胎智能制造体系
双星集团在转型升级过程中积极响应国家政策、率先进行供给侧改革,2017年7月,双星全球领先的轿车胎全流程“工业4.0”智能化工厂全线投产。至此,双星成为全球轮胎行业唯一一家同时拥有卡客车胎和轿车胎全流程“工业4.0”智能化工厂的企业。双星轮胎智能工厂按照工业4.0标准规划建设,采用世界一流生产技术,现代化的物流生产布局,力求做到个性化定制订单的柔性生产,满足互联网时代用户对产品和服务的需求。智能工厂集成了全球最先进的信息通信技术、数字控制技术、智能装备技术,并对原有的轮胎工艺流程进行创新,实现了智能炼胶、智能敷贴、智能成型、智能氮气硫化,以及智能分拣、检测、输送、仓储等30余项工艺流程的升级,实现轮胎全流程管理。
图4 双星“工业4.0”轮胎智能化工厂车间实景
投产以后,通过CPS系统,实现轮胎生产和管理信息的全程可视化。工艺数据自动采集达到98%,自控投用率达到96%,产品不良品率降低80%,劳动生产率提高200%(图3)。企业智能化水平显著提升。可以打破欧美的技术壁垒,质量达到世界高端水平。同时,与这条智能生产线相配套的双星智能服务平台正不断完善。
图5 2016年4月18日中央电视台《朝闻天下》报道:项目实施后,产品不良率降低80%
3)汽车后市场智能运维服务生态圈
为响应供给侧改革,实现由传统制造向服务型制造转变的发展战略,建立了面向终端用户的“O+O”汽车后市场电子商务服务平台。通过双星轮胎切入,以模块化设计、个性化定制满足轮胎行业的创新设计,集成SCM、CRM系统,建立直面用户的开放服务体系,搭建以订单流带动物流、资金流、服务流的全流程服务平台,涵盖传统轮胎、救援、汽车后市场等第三方全产业链服务产品,打通线上线下全流程,实时可溯自动无缝链接,利用大数据分析,转用户满意度为忠诚度,进而重复购买、推荐购买和交叉购买,实现双星独创的差异化“双星物联网生态圈服务平台”的建设和运营。
4)两圈融合,形成物联网生态圈
双星“智能服务”和“智能制造”两圈建成后,相互融合,形成物联网生态圈。“智能服务”生态圈内的轮胎创客网不仅可以与用户进行交互,而且可以整合全球的研发资源。星猴服务网及E+E网络体系,不仅可以为双星轮胎服务,还可以为其他品牌的轮胎及汽车后市场服务。“智能制造”生态圈不仅可以为用户创造高端、高差异化、高附加值的产品,而且可以为行业提供智能装备、整体方案和标准服务。
3、效益分析
本项目核心是实现用户大规模定制,在产品模块化和生产精益化基础上,集成并开发全球最先进的信息通信技术、数字控制技术、智能装备技术,实现企业互联化、组织单元化、加工自动化、生产柔性化、制造智能化。率先建立全国轮胎行业的智能制造样板工程,创造中国轮胎行业的世界名牌,包括服务名牌、轮胎名牌和智能装备名牌。
(1)项目生产工艺数据自动采集达到98%,工厂自控投用率达到96%以上,整个生产过程透明化和可视化,建立了全生命周期数据统一平台,从而实现了智能定制、智能排产、智能送料、智能检测、智能仓储和智能评测。项目实施后,运营成本降低约30%,产品研制周期缩短约50%,生产不良率降低80%以上,劳动生产率提高200%,能源利用率提高约30%,成为行业转型升级的样板。
(2)绿色轮胎智能制造工厂的建设有利于提高轮胎制造业生产效率、提升轮胎制造水平、促进安全生产和节能减排。同时企业通过智能装备,结合先进制造工艺,能够大幅度提升轮胎均匀性、动平衡,降低轮胎滚动阻力和噪音,提高轮胎抗湿滑性能,缩短轮胎刹车距离,延长轮胎寿命。应用该工艺制造出的轮胎可以达到欧盟、美国等国家的标签法规定的标准,符合绿色轮胎要求,推动了“美丽中国”的建设。
(3)通过轮胎行业智能制造体系的搭建,开展智能制造标准体系研究,建立智能评价体系,将智能工厂通用技术要求标准化,搭建起基础标准试验验证体系。标准化的智能制造模式可通过智能工厂模型搭建,再加入通过技术(包括视觉技术、智能传感器、信息自感知、网络通过技术)、工业物联网、工业云服务模型、工业大数据服务、工业互联网架构等,能够在轮胎行业和其他重点领域快速复制并推广应用。
未来发展规划
面对新的机遇和挑战,双星将积极响应中央将国有企业做强做优做大的号召,实施“中国制造2025”和“互联网+”,加快建设和发展工业互联网,推动互联网、大数据、人工智能和轮胎行业的深度融合,全面提升企业研发、生产、管理和服务的智能化水平,促进轮胎产业智能制造踏上新台阶。通过连续性创新和颠覆性创新,实现由满足需求到创造需求,提高我国轮胎在全球的话语权。
声明:本文来源:PLM之神,转自:中国两化融合服务联盟, 由《智能制造》公号整理分享大家,仅供学习使用,不得用于商用,引用或转载请注明出处!如有侵权请联系我们(mfg2025@qq.com)删除!
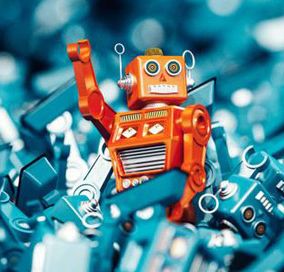
我们专注“软件革命”和“硬件进化”所驱动的工业创新,希望与各位共同见证新智能时代!
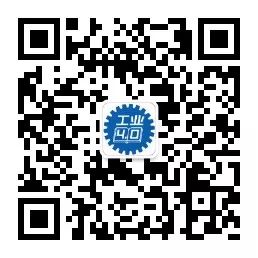
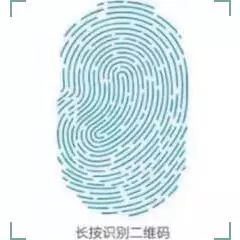
共有条评论 网友评论